Step 1: Silicon is Extracted from Sand
Virtually all solar panels are made of silicon. Silicon is the main component in natural quartz sand (sand-sand or gravel as it is called in Nigeria). Silicon as it is found in sand, in the form of silicon dioxide, is the second most abundant element on earth after oxygen. Silicon sand finds its most important use in building construction. It is also used in the making of high-grade glass, non-ferrous metals, in water purification, in the manufacture of foundries, in the making of semiconductors and transistor parts, in the making of silicones which have wide-ranging applications, in the ceramics industry and in the oil and gas industries. Et cetera. Silicon has one its most significant uses in the manufacture of solar cells.
The first step is converting raw sand (silicon dioxide) into high-grade pure silicon. This conversion process otherwise called Carbon Arc Welding involves placing the sand mixed with carbon into an electric arc furnace and heating it to temperatures beyond 2,000°C. The goal is to remove the oxygen from the silicon dioxide to give pure silicon. This is done by burning the oxygen off with carbon into carbon dioxide. The final product of the process is molten silicon.
Step 2: The Extracted Silicon is Further Purified
The molten silicon produced from Step 1 is just 99% silicon. It is further purified to give a silicon that is 100% pure silicon. The method used here is called the Floating Zone Technique. This involves passing an rod of impure silicon through a heated zone several times in the same direction. The goal is to drag the impurities towards one end with each passing of the rod. At a specific point, the silicon is deemed pure and the impure end is then removed.
Step 3: The Silicon is Doped With Boron or Phosphorus
Doping is a way of artificially adding boron or phosphorus to the silicon. The goal is to create a positive-negative junction along which electricity can flow and to let the silicon itself act as a semiconductor.
N-type and P-type Doping?
When a silicon is doped with phosphorus, it is an n-type cell and when it is doped with boron, it is a p-type silicon.
The main difference between p-type and n-type solar cells is the number of electrons. In a p-type cell, the silicon wafer is doped with boron, an element with one less electron than silicon. This makes the cell positively charged. In an n-type, the cell is doped with phosphorus, which has one more electron than silicon, making the cell negatively charged.
Traditionally, silicon is doped at this stage. Doping at a later stage in the manufacture processes is a recent technology. This is done by using a small particle accelerator to ‘shoot’ the phosphorous ions into the ingot. This new process has not yet become the mainstream.
Step 4: The Silicon Is Made Into an Ingot
After the doping, the doped silicon is re-melted and extracted into a single ingot through a process called the Czochralski method. This process is named after a Polish scientist Jan Czochralski, who accidentally invented the method in 1915 following his accidental discovery that when he mistakenly dipped his pen into molten tin instead of his inkwell, he drew out a single crystal of tin.
This process works exactly in the same way as Mr Czochralski's pen. A seed crystal is dipped into the molten silicon. It is then slowly pulled upwards and rotated simultaneously while being pulled up. During the process, conditions like temperature, rate of pulling and speed of rotation, are controlled to give a large cylindrical ingot from the molten silicon.
Step 5: The Ingot is Made Into Wafers
The round ingots are cut into slices using a diamond wire saw, or recently, with laser beams, into rods of either rectangular or hexagonal sizes. The choice of either of the two shapes is so they can be fitted together without losing any space. Around a half of the silicon is lost in this stage.
The silicon wafers are checked again for any impurities or damage. They are then split and cleaned with industrial soap. This removes any metal residues, liquids or other production remains from the surface that would otherwise impact the wafer’s efficiency.
After the wafer is treated and textured it undergoes an acid cleaning. This removes any post-texturing particles that remained. Both hydrogen fluoride and hydrogen chloride are used during the acid clean.
Step 6: Step 3 Performed At this Stage Instead of At Stage 3
The doping as in Step 3 can be performed at this stage. Instead of the phosphorus or boron to be added to the molten silicon, they can be coated with a layer of boron or phosphorus to from the positive-negative junction.
Step 7: The Cells of Silicon Wafers Are Connected Together With Electrical Wires or Busbars
Electrical contacts that allow the current to flow through the cells are used to connect each solar cell to the other, as well as to the terminals. These electrical contacts are called busbars and fingers. The purpose of busbars and fingers is to conduct the current generated by the cell to the terminal from where it can be inverted and used.
The busbars are the more visible of the two while the fingers are the super-thin of the two wires. The fingers are laid at right angles to the busbars. The fingers collect the generated DC current and deliver it to the busbars which then deliver it to the terminals of the panels in the junction box.
Traditionally, solar panels come with just 2 busbars per solar cell, but advances in solar technologies have given rise to more-efficient cells with up to 6 busbars. Most manufacturers have moved even farther from the traditional 3 busbars to 5 or 6 busbars. LG, REC, Trina Solar, and Canadian Solar have gone ahead of others and developed (multi-busbar) MBB systems using up to 12 or 16 very thin round wires rather than flat busbars.
These electrical contacts are often emblazoned onto the surface of the solar cells through a process called screen printing. The printing process involves the vacuum-evaporation of the metals through photoresist that are then silkscreened onto the cell or deposited directly on the exposed portion of cells that have been partially covered with wax. Metals used in the making of these busbars and fingers include palladium, silver, nickel or copper. They are made from very thin wires so as to not block the cells from receiving sunlight. After the contacts have been put in place, thin strips or metallic fingers are then placed between the cells.
A matrix of 60 or 72, 96 to 144 different cells are linked together with busbars in series to form the module.

Step 8: The Cells Are Coated
The cells themselves can reflect away up to 35% of the sunlight that falls on their surface. To reduce this loss, an anti-reflective coating is laid on the silicon wafer. The most commonly used coatings are titanium dioxide and silicon nitride, though others like graphene, are used.
The goal of the anti-reflective coat is to increase efficiency of the cells and also their performance over their lifespan by reducing losses due to the cells reflecting away incident sunlight. As a bonus, the anti-reflective coating gives the modules their aesthetics while reducing the glares that fall off them.
Step 9: The Cells Are Sealed And Framed
The finished solar cells are sealed into silicon rubber or ethylene vinyl acetate (EVA) polymer encapsulant on both sides. After the cells are put together, a thin layer (about 6-7 mm) of glass is added on the front side of the panel, the part that faces the sun. The encapsulated solar cells are then placed into an aluminium frame with a back-sheet and a glass or plastic cover.
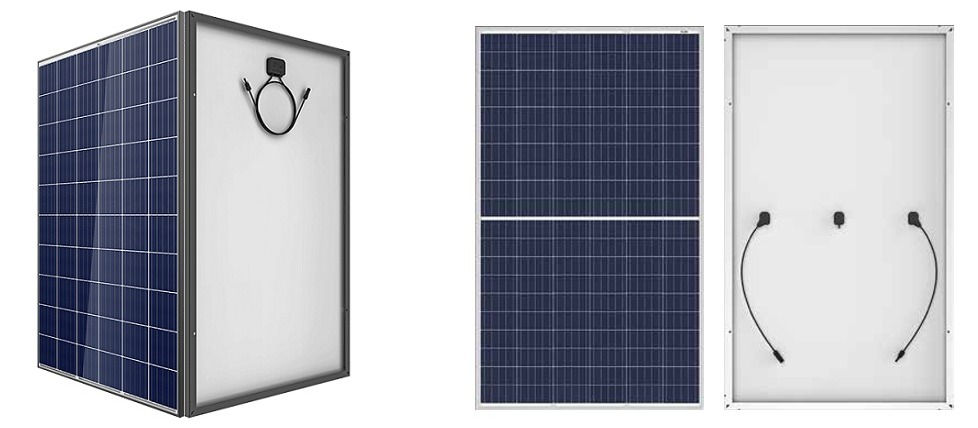
The goal of the backsheet is to prevent water, oil and other materials from entering the panel from the back. It also provides a holder for the junction box where the cells can be connected to a terminal.
SolarKobo helps its clients in Lagos and throughout Nigeria make the best possible choices of solar panels and other solar electricity products. We also have university-trained engineers who provide the best possible installation services on order.
Commentaires