Inverter Welding Machines
- SolarKobo
- Sep 14, 2020
- 3 min read
Updated: Jan 16, 2021
Welding machines or 'welders' as they are popularly known are electrical devices that generate heat with the help of electric current that melts metal parts, so that these parts can be joined together. Traditionally, welding machines work by creating an electric arc between a metal stick or electrode and a base material to melt the metals at the point of contact.
Inverter welders are by far a better option for users everywhere in Nigeria.
How Inverter Welders Work
An inverter welder is a relatively new and innovative type of welder and by far more sophisticated and generally more efficient.
Like all inverter-based systems, inverter welding machines work as 'rectifiers' and then as inverters. First, they rectify the AC power from the mains to DC. Second, they switch or invert the DC power through a stepdown transformer to produce the desired welding voltage or current.
The most important feature in inverter welders is a high-power semiconductors known as the insulated gate bipolar transistor (IGBT). These transistors in an inverter based machine are controlled by a microcontrollers so that the electrical characteristics of the welding power can be changed by software in real time, even on a cycle by cycle basis, rather than slowly over hundreds if not thousands of cycles. This gives inverter welders a high switching frequency, up to 10kHz or higher.
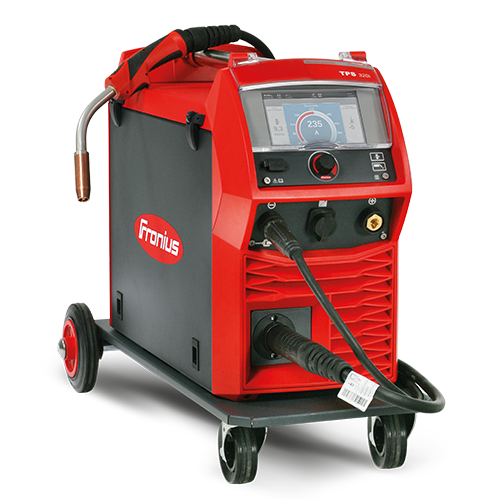
General Features And Advantages Over Conventional Welding Machines
The most important feature of inverter welders is that they can are controlled only through software. The controller software implements features that cannot be installed in transformer-based welders, for instance, pulsing the welding current, providing variable ratios and current densities through a welding cycle, enabling swept or stepped variable frequencies, and providing timing as needed for implementing automatic spot-welding.
New features can be added to a software-controlled machine if needed, through a software update, rather than through having to buy a more modern welder. This makes them 'intelligent welders'.
Other features of inverter welders which gives them a comparative advantage over conventional welders include:
Lesser Weight and Size: The use of microcontrollers reduces the bulk of the step down transformer, as the mass of magnetic components (transformers and inductors) that is required for achieving a given power level goes down rapidly as the operating (switching) frequency is increased. This generally reduces the overall size of the welders. They are also easier to move.
Higher Efficiency: Quality inverter machines, will have an efficiency rating of about 80-90% while conventional welders have a significantly lower efficiency of about 50%. This is due to the fact that the larger transformers in conventional machines have greater resistance and therefore lose a significant amount of power (or energy) through heat dissipation. In other words, unlike conventional welders, they save more energy.
Use of Generator Power: It is capable of being run on smaller portable generators--something that is often not possible with traditional transformer machines.
High Duty Cycle: Generally much higher duty cycles are achievable with inverter-based machines, again due to the difference in transformer size. Although the smaller components in an inverter machine heat up quickly, they can be cooled much easier and faster.
DC Output: Many conventional welders only have AC output, which means they are limited in the types of electrodes they can weld with. However, with inverter-based machines the current is much more easily rectified into DC which means they are able to weld a wide range of different welding electrodes. It also means that some inverters are also suitable for DC welding, which is not possible with conventional AC machines.
Performance: The performance of quality inverter-based welders is substantially superior to that of conventional welders.
Protection: The inverter circuitry also provide features such as power control and overload protection.
Plug and use: They are made to be used without any tools. They are able to known which components are connected and will warn of any incompatibility. As very intelligent systems, misadjustments are ruled out.

Disadvantages
The chief disadvantage of inverter welders is the price. Inverter welders are by far more expensive than traditional welders though they give a full return on investment on the long run.
Unlike is suggested by the name 'inverter welders', they do not come with pre-installed batteries and still have to depend on grid power. They are, in the proper sense, 'inverter-based welding machines'. In this sense, they use a series of electronic components to convert the power - in contrast to conventional transformer-based devices which depend primarily on a single large transformer to regulate the voltage.
Also, a technical knowledge of production debugging and parameter control and of the use of softwares generally, is required for its operation. They are thus made for professional welders. SolarKobo helps its clients in Lagos and throughout Nigeria make the best possible choices of inverters and inverter-based systems.
Comments