Parts of A Solar Panel
- SolarKobo
- Apr 5, 2021
- 4 min read
1. Solar Cells
Solar cells do the major work of converting sunlight directly into electricity. They are often rectangular or hexagonal wafers of purified and crystallized silicon over which a network of very thin wires called fingers/ribbons and busbars have been connected to conduct away the electricity generated from the cells to the terminals where they can be used by appliances.
Solar cells come in different designs, colours, technologies and configurations. When these cells are arranged together and connected with busbars and fingers in sizes of 60, 72, 96, 120 and 144 cells or more, they form a solar module.

2. EVA Film
EVA ‘ethylene vinyl acetate’ is a specially designed polymer and highly transparent plastic layer used to encapsulate the cells and hold them in position during manufacture. They serve to protect the cells from adverse weather conditions. They also help prevent moisture and dirt from entering the solar panel. In addition, they help to soften the impact of shocks and vibrations and therefore protect the solar photovoltaic cells and the busbars and fingers. These cells are placed between two EVA films in a vacuum and, under heat and compression and with the help of a special type of lamination machine, are laminated together .

There are two major problems that are often associated with the EVA film and both can impact the solar panel module:
1. Delamination
In delamination, the EVA film starts to separate from the glass and backsheet. This allows air and moisture inside the solar PV panel resulting in corrosion. This problem is often due to failures in the lamination process.
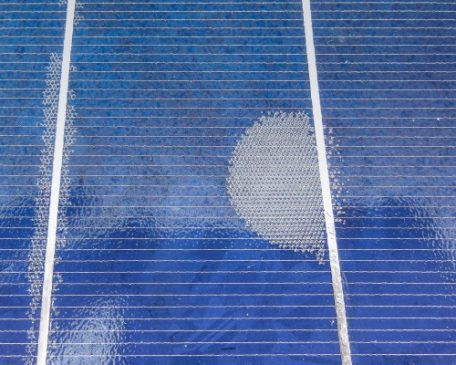
2. Browning
Browning is a change in colour of the EVA film. This occurs when certain additives used to prevent browning and enhance UV resistance start to disappear. A solar panel can also brown if it is stored or handled poorly. It can cause bleaching and blistering at the EVA film and the solar backsheet, resulting in the rusting of the solar cells underneath them.
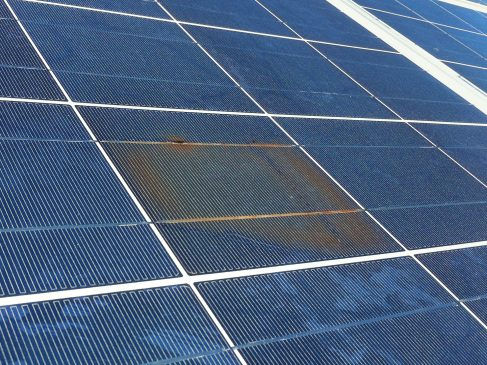
3. Glass Sheet
After the encapsulation of the solar cells in the EVA films, a glass sheet is placed over the front side of the panel where the cells interact with sunlight.
The glass protects the cells that are constantly exposed to weather, dust, rain and hail. The glass is often a high-strength tempered glass about 3-4mm think designed to resist mechanical loads and extreme temperatures. The IEC minimum standard impact test for all solar panels requires these glass sheets be able to withstand an impact of hail stones of 1 inch diameter traveling up to 60 mph.
Also, the cells themselves can reflect away up to 35% of the sunlight that falls on their surface. To mitigate this, the rear side of this glass is coated with anti-reflective chemicals like graphene, titanium dioxide and silicon nitride to prevent losses of this nature and by so doing, allow more sunlight to reach the cells and improve the efficiency of the panels.

4. Aluminium Frame
The aluminium frame protects the edges of the laminated section enclosing the cells. The frame also provides a solid structure to help their mounting and keep the panels in shape and position. They are often designed to be lightweight, stiff and able to withstand extreme stress and loading from high wind and other weather impacts. The aluminium frame contributes a very significant amount of the weight of the solar module.
The aluminium frame can be silver or anodised black. It can also be coated with other elements like silver or nickel. Depending on the manufacturer, its corner sections are made to either be screwed, pressed or clamped together during assemblage to provide different levels of strength and stiffness.
5. Back Sheet
A backsheet is added to the rear of the panel. It acts as a moisture barrier and a skin for mechanical protection and electrical insulation. It is made of different types and grades of polymers or plastics each offering different levels of protection, thermal stability and long term UV resistance.
The backsheet layer is typically white in colour but is also available as transparent or black depending on the manufacturer and the design of the module.
5. Junction Box
The junction box is a small weather-proof enclosure in the form of a black box located on the rear side of the panel. It is needed to securely attach the cables required to interconnect the panels. The junction box is important as it is the central point where all the cells are interconnected and must be protected from moisture and dirt.
All junction boxes have bypass diodes that keeps electricity flowing in one direction and prevent it from feeding back to the panels. Bypass diodes can fail over time and may need to be replaced, so the cover of the junction box is usually able to be opened or removed for servicing. However, as modules have changed, junction boxes have had to improve their ability to perform their functions. Many modern solar panels now use more advanced long lasting diodes and non-serviceable junction boxes.

6. Connectors
Almost all solar panels are connected together using special weather-resistant plugs and sockets called MC4 connectors. The term MC4 stands for multi-contact 4mm diameter connector. Due to the extreme weather conditions the connectors are built to be very robust, secure, UV-resistant and to maintain a good connection with minimal resistance at both low and high voltages up to 1000V.
SolarKobo helps its clients in Lagos and elsewhere in Nigeria make the best choice of solar panels. SolarKobo also has university-trained engineers that provide the best installation services on order.
Comments